One of the most important aspects of owning and/or operating a
car lift is performing periodic maintenance. We pride ourselves on making our lifts (two-post, four-post, etc.) as low-maintenance as possible, but there are still a few chores you’ll need to complete from time to time. All of this is listed in your owner’s manual, of course, but we’d like to offer a fresh reminder.
Required Monthly Maintenance
Remember this little gem from your manual? You should! Even a rugged
BendPak two-post or four-post lift needs a little love now and again. If you’re currently having an “oh, shoot” moment, but you didn’t say “shoot,” go ahead and finish this article, then go make yourself a little inspection and see how your lift is holding up.
The Monthly List
- Check all arm adjusting locks for proper operation.
- Check all cables connections, bolts and pins to ensure proper mounting and torque.
- Visually inspect safeties for proper operation.
- Lubricate posts with grease.
- Inspect all anchors bolts and retighten if necessary.
- Check all posts for squareness and plumb (straight) fit.
- Inspect all pivot arms pins making sure they are properly secure.
- Check cable tension and adjust if necessary.
- If the lift is equipped with overhead micro-switch, check for proper operation.
Wire Rope Inspection and Maintenance
We’ll spend the rest of this article on how to inspect the cable system.
All lifting cables should be replaced every three to five years or when damage is visible. The better you take care of your cables, the longer they’ll last. One of best things you can do is keep your cables lubricated with 90-WT gear oil or ALMASOL® Wire Rope Lubricant. These oils/lubricants get deep into the fibers to prevent damage. Lubricate your cables every three months (four times a year). Mark it on your calendar at home or work to remind you when it’s
car lift and cable maintenance time.
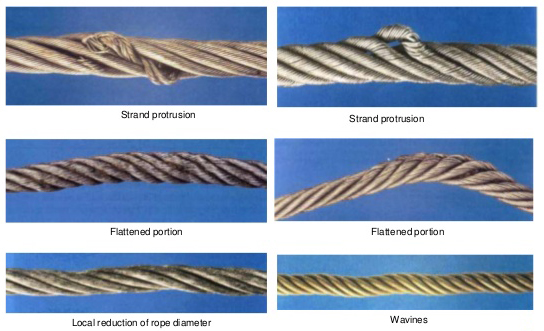
Since you’re right there anyway when your lift is in use, take that easy opportunity to inspect your cables. This takes what, a minute or less per column? If there’s damage on any cable, remove it and replace it immediately. Don’t risk everything just to finish an extra job or two. So, does that mean we’re telling you to replace every cable that’s been discolored or looks “less than brand new” after a year or two of heavy use? Not necessarily!
A little wear is to be expected over time. Here’s our official, factory-recommended rule-of-thumb: if in the course of a single day, you see six random wires sticking out over the length of a single cable (when examining all strands), the entire cable needs to be replaced. Additionally, if you see three broken wires in just a single strand over the course of a single day, you also need to replace the entire cable.
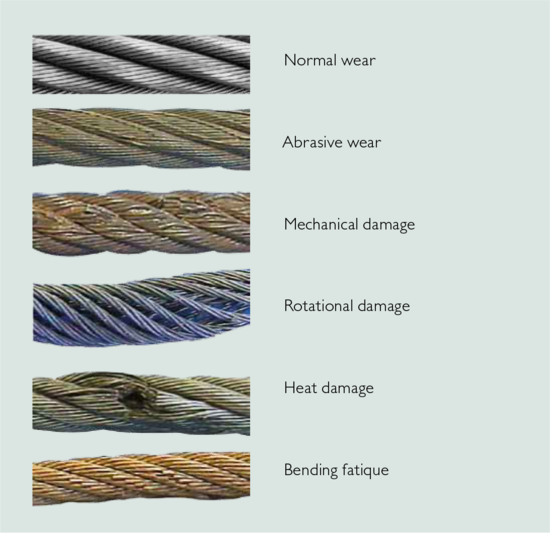
In other words, when you start to see wires sticking out of strands, whether they’re all on a single strand or spread out along the length of the entire cable, you need to replace that cable. You don’t necessarily need to replace good cables that just happen to be near the defective cable(s).
How Do I Look for Cable Damage?
1) Relax your rope to a stationary position and move the pick-up points off the sheaves. Clean the surface of the rope with a cloth or a wire brush, so you can see any breaks.
2) Flex the rope to expose any broken wires hidden in the valleys between the strands. Look for broken wires. One way to check for crown breaks is to run a cloth along the rope to check for possible snags.
3) With an awl, probe between wires and strands and lift any wires that appear loose. Evidence of internal broken wires may require a deeper rope examination.

Note: awls and owls are different things
Be Your Own “Cable Guy”
While some wear is to be expected over time, once the cable has worn down by 10% of its original size, it needs to be replaced. So if your original cable is .5” in diameter, it should be replaced once it reaches .45”. That difference may seem small, but 14,000-lb. rated cable that loses 10% tensile strength will be rated at 12,600 lbs., assuming no other structural damage. This is a big difference in any circumstance but especially when lifting heavy-duty vehicles.
If the wires appear to have corrosion, pits or kinks, or if there is evidence of kinking, crushing, cutting, bird-caging or a popped core, the cable needs to be replaced. Also look for evidence of heat damage.
Cable Sheaves and Guide Rollers
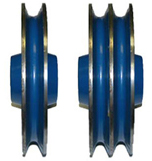
Any points at which the cables make contact with the sheaves need to be inspected. Look for signs of wear. If the surface has been compromised or made rough, it’s going to affect your cables. Checking these parts is easy: simply look and lubricate. The sheave axles take standard wheel bearing grease, and the sheaves and guide rollers take 90-WT gear oil or similar heavy lubricant. To get the oil on, you can pump it, spray it, brush it, smear it on by hand or swab it. Just keep it greasy. Do this every three months at the same time you inspect your cables (to keep things easy). Make a thing of it. Have a car lift cleaning party. Bring cake?